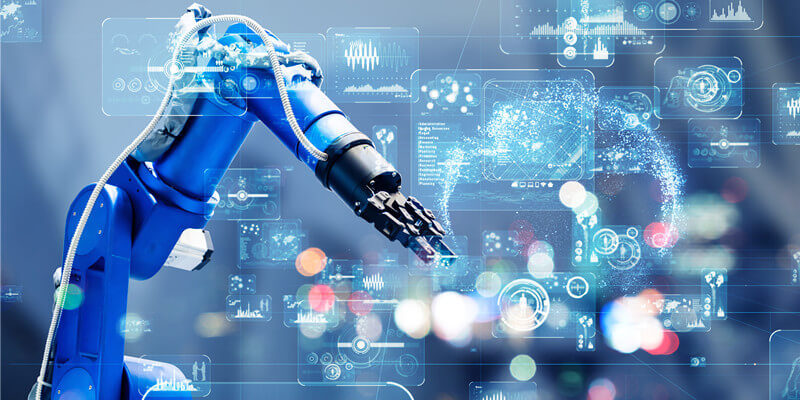
5 Major Advantages You Get From Cold Forging
March 29, 2021
5 Major Advantages You Get From Cold Forging
No doubt that cold forging is increasingly becoming the most popular forging method in the market. There are many reasons for this development, and one of them is the major benefits that the technology is offering to the market. That’s why most manufacturers, as well as machine users, are opting for cold forged products.
If you wonder what kind of benefits you get from cold forging, this guide is for you. We have rounded up some of the major advantages that are associated with cold forging. Here are the major advantages of cold forging:
Enhanced Mechanical Properties
One of the biggest advantages of cold forging is the improved mechanical properties of the forged products. Because of the high dimensional stability that the forming process produces, the forged produce does not change to any structural changes. It keeps the original mechanical and tensile characteristics hence the higher mechanical properties. That’s why cold forged parts can withstand demand conditions better.
Better Surface Finish
Another advantage of cold forging is the better surface finish. The high-quality forging sequence that the process offers eliminates most of the deformities that come with other forging methods. This means the produced machine parts are near-net shapes; hence there is no need for the post-forging process. If there is any, then it is not that intense and expensive.
Lower Production Cost
Another reason why cold forging is growing popular in the market is the reduced production cost. If you look at the forging process, you will find out that some of the steps in other forging processes are eliminated. A good example is the pre-heating stage in hot and warm forging. The finishing step is also significantly reduced with cold forging. All these cases reduce the cost of production.
Fast Production
The speed of production is an important factor, especially if you are in the business. You need a forging process that produces high volume in unit time. That’s what cold forging offers. Because some of the steps have been removed, the speed of production is significantly reduced. This means more output, more money in terms of profits.
Minimal Material Wastage
The material that goes to waste when forging is a loss to your business. This includes the material that you trim off when finishing the forged products. With cold forging producing near net shapes, the material wastage is significantly reduced. This is definitely one of the biggest advantages of cold forging.